When comparing cold-formed steel home kits to red iron buildings, consider this: Cold-formed steel structures offer quicker construction timelines and cost efficiency. They are durable, easy to maintain, and recyclable. On the other hand, red iron buildings provide more customization options for larger facilities. Understanding the distinct advantages each material offers is crucial for making well-informed construction decisions. Ultimately, the choice between cold-formed steel home kits and red iron buildings depends on your project requirements, budget, and timeline. Making a well-informed decision guarantees the success of your construction project.
Key Takeaways
- Cold-formed steel home kits offer quicker construction timelines and cost efficiency.
- Red iron buildings provide extensive customization options for larger facilities.
- Cold-formed steel structures have minimal maintenance needs and resist rust and corrosion.
- Red iron buildings excel in open-span structures due to their strength and durability.
- Combining both materials can balance speed and customization for diverse construction projects.
Material Overview
When considering steel home building options, a fundamental understanding of the materials used is essential to make informed decisions for your construction project. Two prominent options stand out in the steel construction domain: red iron buildings and light gauge steel structures. Red iron buildings are characterized by their durability and strength, achieved through the use of large wide beams coated with red iron oxide for protection against corrosion. On the other hand, light gauge steel, commonly found in cold-formed steel home kits, offers a more customizable approach to construction. Light gauge steel sheets are used for framing components, providing structural rigidity while allowing for intricate design possibilities.
Red iron buildings excel in projects requiring vast open spans and rectangular shapes, such as gyms or churches, due to their robust primary and secondary framing members. In contrast, light gauge steel construction, though requiring specific engineering solutions, enables tailored designs to meet individual project requirements. Understanding the distinctions between these steel building materials is vital in selecting the most suitable option for your construction needs.
Steel Buildings Defined
Steel buildings encompass structures constructed using various steel materials, offering durable and versatile solutions for diverse construction projects. When considering steel buildings, understanding the key features that define this construction method is crucial:
- Iron Steel Composition: Traditional steel buildings utilize iron steel, which is renowned for its strength and durability. This material provides structural integrity and stability to the building, ensuring long-term resilience against various environmental factors.
- Versatility in Design: Steel buildings offer a classic yet flexible design approach, allowing for customization based on specific project requirements. From simple rectangular structures to more intricate architectural designs, steel buildings can adapt to various construction needs.
- Efficiency in Construction: Compared to other construction methods, steel buildings are recognized for their efficiency in the building process. The use of iron steel components enables faster construction timelines, making it a preferred choice for projects requiring timely completion without compromising quality.
Understanding Red Iron
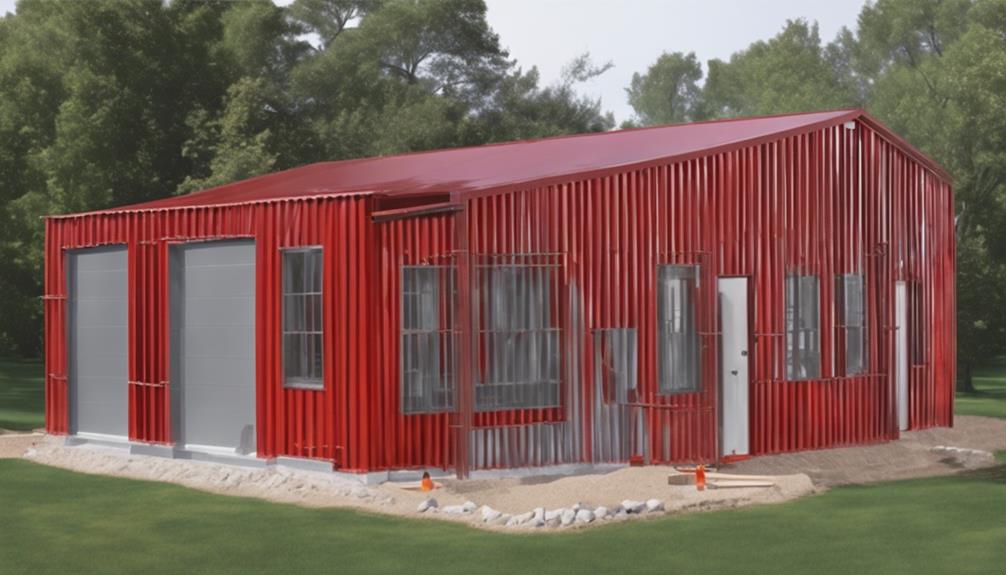
Red iron buildings, characterized by using industrial-grade steel with a red iron oxide primer, offer enhanced protection against corrosion. The structural support in red iron buildings is primarily provided by red-painted steel beams and columns, ensuring robustness and longevity. These steel beams play an important role in maintaining the overall stability and integrity of the structure. The red iron’s strength and durability make it a popular choice for various construction projects where resilience is paramount. It is essential to accurately match red iron kits with concrete slab sizes to streamline the construction process and avoid the need for extensive on-site modifications. Skilled welders and precise computer-aided design are necessary during the manufacturing phase of red iron buildings to guarantee accuracy and quality in the final product. Embracing the use of red iron for your building projects can provide you with a reliable and cost-effective solution for your structural needs.
Construction Timeline
Considering the differing construction timelines, it is evident that cold-formed steel home kits offer a more efficient and expedited building process compared to red iron buildings. Here are three key points to highlight this advantage:
- Efficiency: Cold-formed steel home kits are known for their streamlined construction process, allowing for a quicker turnaround from start to finish.
- Speed: While red iron buildings may take considerably longer to construct due to customization and complexity, cold-formed steel home kits can be erected in just a few months.
- Project Completion: The construction timeline for red iron buildings can be up to five times longer than that of cold-formed steel home kits, showcasing the efficiency and speed of the latter option.
With these factors in mind, opting for a cold-formed steel home kit can provide a faster and more efficient construction timeline, meeting the needs of homeowners looking for a timely completion of their projects.
Building Process: Steel
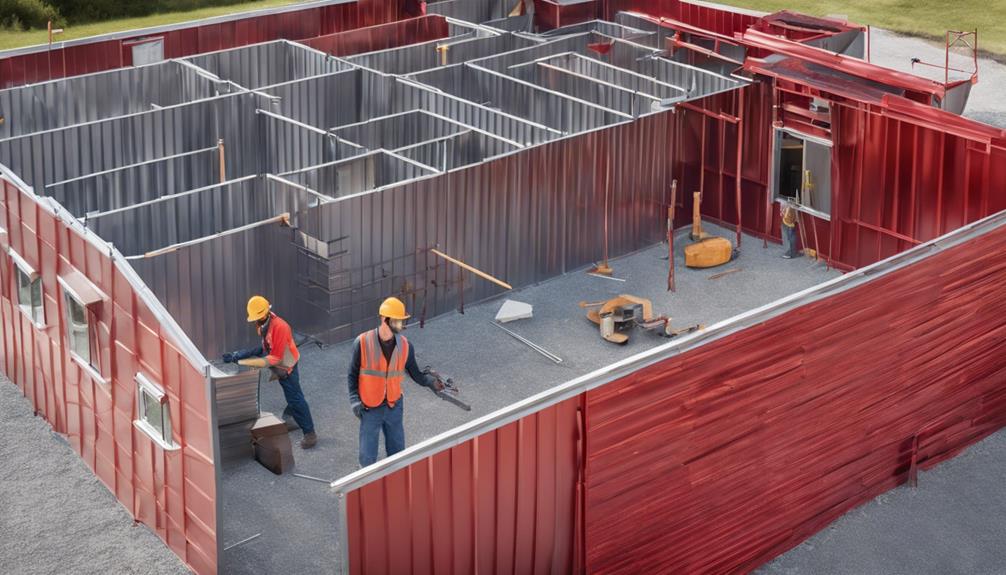
When constructing steel buildings, the primary framing components utilized include I-beams, tubing, and sheets. Steel framing offers a sturdy and versatile solution for construction needs. Steel buildings, whether using red iron or light gauge steel, provide exceptional durability and resistance to various elements, ensuring longevity and safety for your structure. The table below compares steel framing with a focus on customization options for a more tailored design approach.
Aspect | Steel Framing | Red Iron |
---|---|---|
Custom Design | Highly customizable designs | Limited design flexibility |
Strength | Durable and robust | Strong and rigid |
Construction Time | Quick erection in months | Longer construction period |
Resilience | Resistant to natural disasters | Excellent durability |
Versatility | Flexible for various needs | Ideal for specific projects |
Steel framing allows for intricate and personalized designs, making it a preferred choice for those seeking a unique and tailored construction approach.
Red Iron Building Steps
In the construction process of iron buildings, the initial steps involve preparing the site, including clearing the land and leveling the ground for further construction. Once the site is ready, foundation work becomes paramount in ensuring the stability and longevity of the steel building. This step includes excavation, forming, and pouring of concrete to create a solid base for the structure. Following the foundation work, structural steel framing takes center stage, with columns, beams, and trusses being erected to provide the necessary support for the building. This framework forms the skeleton of the steel building, dictating its strength and overall structure. Each step in the red iron building process plays an essential role in creating a durable and functional space. By meticulously following these steps, the construction of steel buildings can proceed smoothly, resulting in a robust and reliable structure tailored to specific needs.
Weather Resistance
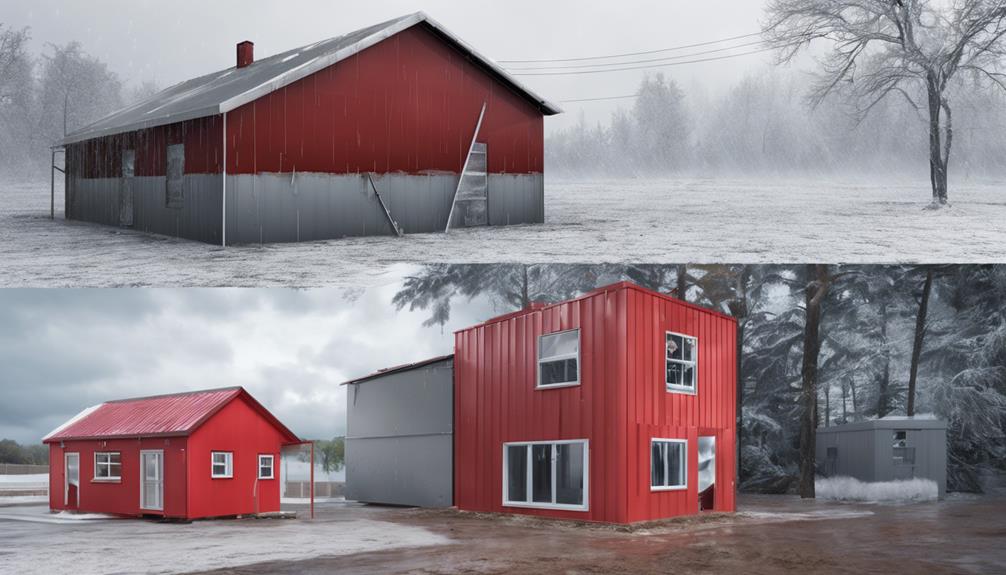
Cold-formed steel buildings demonstrate exceptional weather resistance due to their treated surfaces that effectively combat rust and corrosion. The cold-formed steel construction process involves applying protective coatings that shield the material from environmental elements, ensuring longevity and durability. In contrast, red iron buildings are known for their iron oxide coating, which enhances their resilience to extreme weather conditions. This coating acts as a barrier against corrosion, making red iron buildings highly weather-resistant as well. Both types of structures are designed to withstand harsh weather, with cold-formed steel buildings also offering fire-resistant properties due to their non-combustible nature. Additionally, red iron buildings are praised for their robust framing, which plays an essential role in their ability to endure various weather challenges. Whether facing heavy rains, strong winds, or extreme temperatures, both cold-formed steel buildings and red iron structures are equipped to provide reliable weather resistance for long-term performance.
Pest Resilience Factors
Given the emphasis on weather resistance in both cold-formed steel buildings and red iron structures, it is essential to examine their robust pest resilience factors now. When choosing between steel and red iron structures, understanding their pest resistance capabilities is vital for ensuring the longevity of your building. Here are three key points to ponder:
- Treatment Methods: Cold-formed steel buildings are treated with pest-resistant solutions to deter common pests like termites, safeguarding the structural integrity of the construction.
- Integrated Pest Resilience: Red iron buildings are also designed with pest resilience measures, making them less prone to insect infestations, thereby reducing the need for extensive pest control measures.
- Long-Term Durability: Both steel and red iron structures prioritize pest resistance, contributing to lower maintenance costs and enhancing the overall durability of the building over time.
Design Flexibility
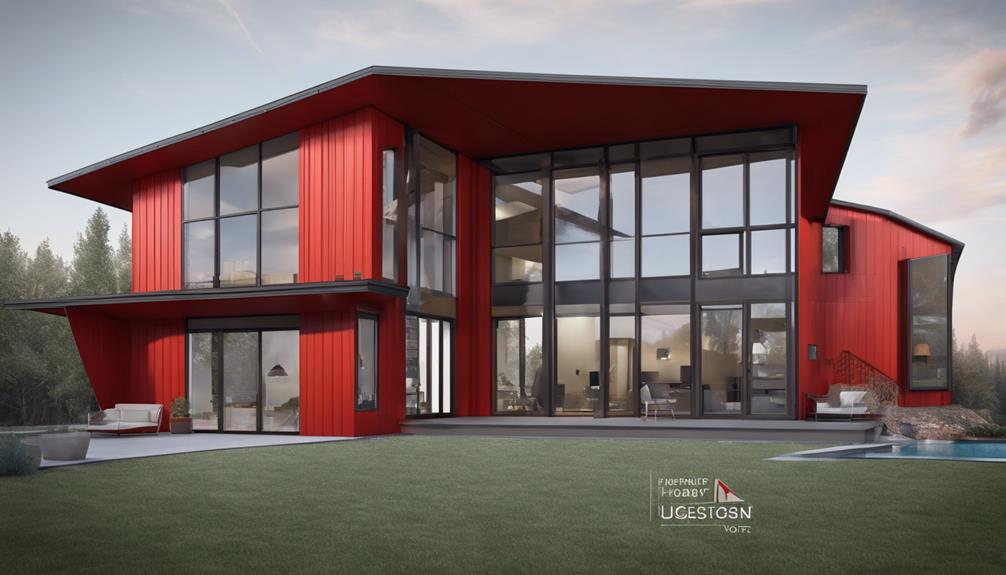
For enhanced design flexibility in steel home buildings, consider the myriad customization options available to tailor the structure to specific needs. Cold-formed steel buildings offer versatility through options like standing seam or gambrel roofs, allowing for unique architectural expressions. These buildings can incorporate features such as mezzanines, monitors, and lean-tos, enhancing functionality and aesthetics. On the other hand, red iron buildings provide customization for larger facilities by supporting mezzanines, lofts, and awnings, catering to diverse spatial requirements. Red iron structures can accommodate various architectural styles and easily integrate large windows and doors for a modern aesthetic. Steel structures, whether cold-formed or red iron, present near-endless opportunities for customization, enabling tailored solutions for specific design needs. By choosing the right building type, you can achieve a personalized space that meets both functional requirements and design preferences in steel construction.
Engineering Solutions
When engineering solutions for steel home buildings, the focus lies on utilizing specific materials to guarantee structural integrity and longevity. In the comparison between steel vs. iron primary framing, each material offers unique benefits for constructing durable and stable structures:
- Light Gauge Steel Sheets: Cold-formed steel home kits primarily use light gauge steel sheets for framing components. These sheets are designed to provide efficient strength and durability while allowing for customizable designs tailored to specific needs.
- Red Iron Beams: Red iron buildings feature large wide beams coated with red iron oxide for increased strength and durability in their engineering. These beams offer robust framing solutions that ensure long-lasting integrity and stability in construction projects.
- Structural Rigidity: Cold-formed steel structures are engineered to provide structural rigidity against natural disasters and harsh weather conditions. This design approach emphasizes the efficient use of materials to enhance strength and durability, making them ideal for withstanding various environmental challenges.
Warranty Comparisons
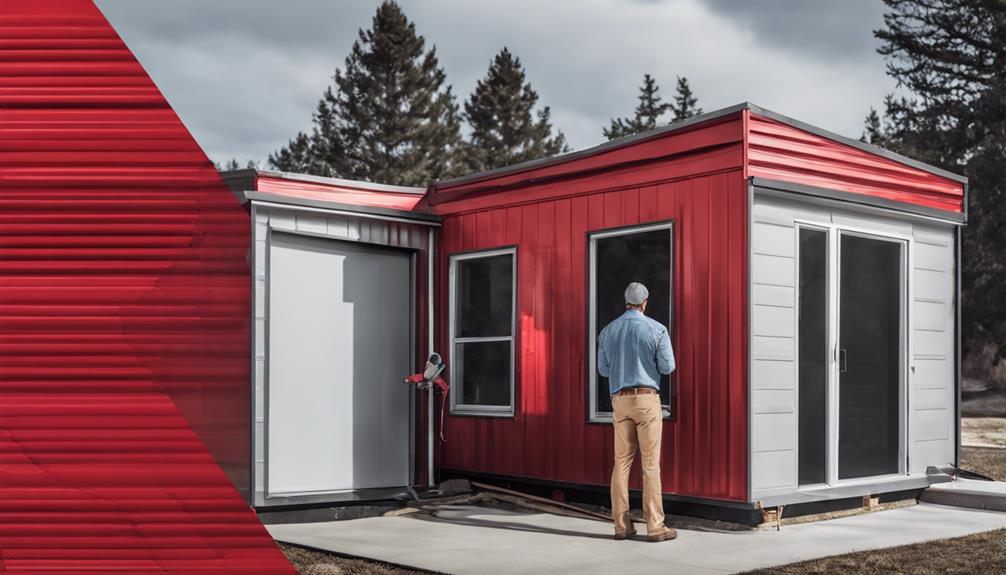
Considering the longevity and coverage of warranties, evaluating the differences between cold-formed steel and red iron buildings is essential for making informed decisions regarding long-term maintenance and support options. Cold-formed steel buildings typically offer warranties lasting up to 40 years, covering important parts like the structural frame, roof, and paint finishes. These warranties guarantee thorough coverage and peace of mind for the structure’s longevity. On the other hand, red iron buildings come with warranties ranging from 20 to 50 years, often including extended coverage for structural integrity and paint coatings. Understanding the warranty comparisons between these two building types is vital for selecting the most suitable option for your project. Whether it’s the steel studs used in construction, the manufacturing plant’s quality control, or other important components, having clear warranty terms for the various parts of the building is fundamental in ensuring the durability and support of your investment.
Cost Analysis
To conduct a thorough cost analysis between cold-formed steel home kits and red iron buildings, customization, size, and location must be considered. When comparing the costs of these two types of metal buildings, it is essential to explore specific aspects to make an informed decision:
- Upfront Costs: Cold-formed steel home kits generally have lower initial costs per square foot due to minimal fabrication needs, offering a cost-effective alternative to traditional construction methods.
- Regional Variances: Red iron buildings may be more economical in certain regions based on factors like availability and manufacturing processes, impacting the overall cost comparison between the two options.
- Long-Term Expenses: While red iron buildings may require a higher initial investment, they often come with longer warranties and increased durability, which could potentially offset the higher upfront cost over time.
Considering these factors alongside customization, size, and location can help in determining the most cost-effective solution for your metal building project.
Structural Durability
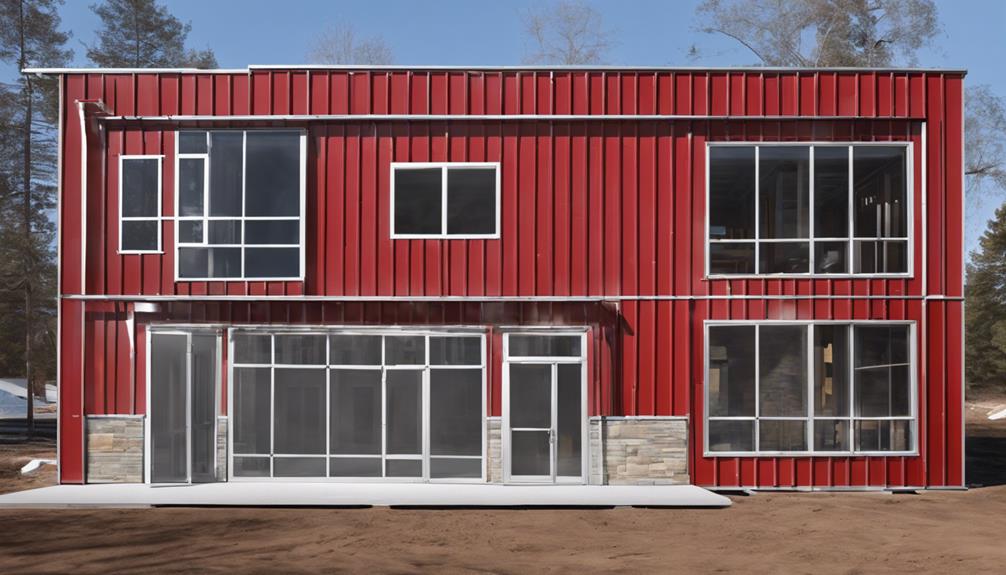
Cold-formed steel buildings exhibit remarkable structural durability, ensuring long-lasting reliability and stability. These structures are engineered to withstand specific loads, such as 30 psf ground snow load and 115 mph wind speed. The robust nature of cold-formed steel buildings makes them comparable to more traditional steel buildings in terms of structural integrity. The deep drilling techniques used in their construction contribute to their strength and resilience. When considering structural durability, cold-formed steel buildings offer something more traditional steel buildings provide, ensuring a sturdy and long-lasting construction solution. Additionally, the labor involved in assembling these buildings plays a significant role in their durability, with proper construction techniques and attention to detail enhancing their longevity. Below is a table highlighting the structural durability aspects of cold-formed steel buildings compared to red iron buildings:
Aspect | Cold-Formed Steel Buildings | Red Iron Buildings |
---|---|---|
Load Capacity | Can withstand specific loads like 30 psf ground snow load and 115 mph wind speed | Known for high load-bearing capacity |
Construction Technique | Utilizes deep drilling for enhanced strength | Relies on traditional construction methods |
Labor Required | Skilled labor involved in assembly for the best durability | Also requires skilled labor for construction |
Energy Efficiency
Enhancing energy efficiency in steel home construction involves optimizing insulation properties and integrating energy-efficient features for a more sustainable living environment. When comparing cold-formed steel home kits to red iron buildings with regard to energy efficiency, several key points emerge:
- Superior Insulation Properties: Cold-formed steel home kits offer better insulation properties compared to red iron buildings, ensuring reduced heat loss or gain.
- Additional Insulation Requirements: Red iron buildings may require additional insulation to match the energy efficiency levels of cold-formed steel homes, potentially adding to the overall construction cost.
- Integration of Energy-Efficient Features: The design of cold-formed steel structures allows for easier integration of energy-efficient features such as solar panels and energy-efficient windows, enhancing the overall energy performance of the building.
Maintenance Needs
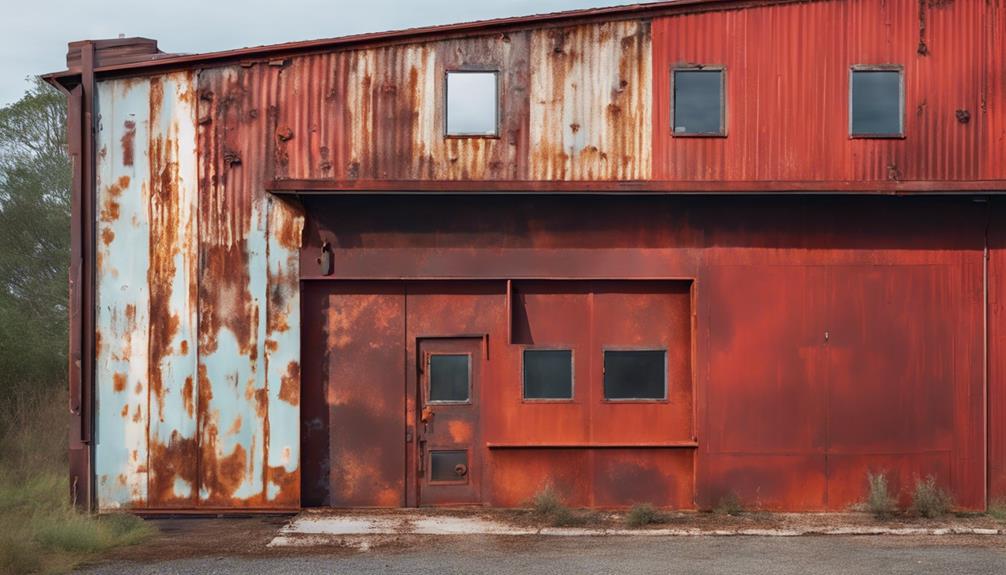
With regards to maintenance needs, it is important to understand the differences between cold-formed steel and red iron buildings. One of these buildings, a cold-formed steel structure, stands out for its minimal maintenance requirements. This is primarily due to their galvanized framing, which effectively resists rust and corrosion. In contrast, red iron buildings may need periodic maintenance to prevent rust and corrosion, especially in high humidity or coastal areas. Regular inspections are essential for both types of buildings, but cold-formed steel buildings generally have lower maintenance needs over time. The galvanized framing in cold-formed steel buildings contributes greatly to their longevity and reduces the need for frequent upkeep. By ensuring proper care and conducting occasional inspections, you can maintain the durability and structural integrity of both cold-formed steel and red iron buildings. These are important things to know when considering the maintenance needs of these construction options.
Environmental Impact
Regarding environmental impact, red iron buildings generally have a larger carbon footprint compared to cold-formed steel home kits. This is primarily due to the more energy-intensive processes involved in the fabrication of red iron buildings, which contribute to higher carbon emissions. On the other hand, cold-formed steel home kits are more environmentally friendly for several reasons:
- Minimal Waste Generation: Cold-formed steel home kits result in minimal waste during both manufacturing and construction phases, reducing the overall environmental impact of the project.
- Recyclability: Cold-formed steel is 100% recyclable, making it a sustainable choice for eco-conscious construction projects. This recyclability factor enhances the overall environmental sustainability of the building materials used.
- Alignment with Green Building Practices: Opting for cold-formed steel home kits aligns with green building practices, helping to reduce the environmental footprint of the construction project. This alignment can appeal to those looking to construct environmentally conscious structures.
Project Suitability
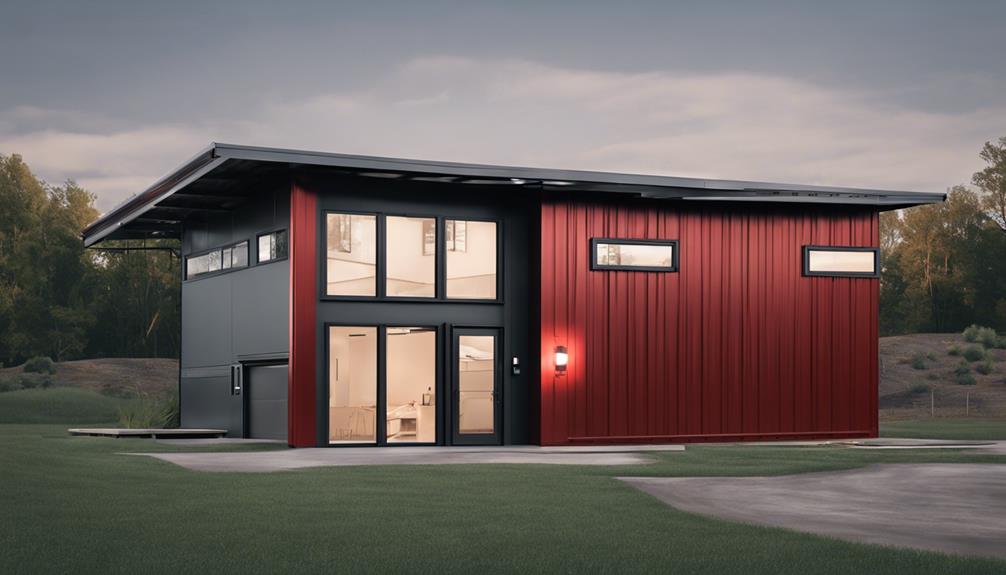
Considering the structural differences between light gauge steel home kits and red iron buildings, project suitability is a critical factor to determine the most appropriate construction method for your specific needs. Light gauge steel home kits excel in projects requiring intricate designs and multiple partitions, offering flexibility for customization. On the other hand, red iron buildings are best suited for large open-span structures like gyms, churches, or industrial facilities due to their durability and affordability. Combining both light gauge steel and red iron can be a viable option for projects with diverse structural requirements, leveraging the strengths of each construction method. Red iron buildings commonly utilize steel or aluminum panels for cladding, enhancing both their durability and aesthetic appeal. In contrast, light gauge steel buildings provide flexibility in cladding options thanks to their standard framing, allowing for a wide range of design choices. Understanding these distinctions is key to selecting the most suitable construction approach for your project’s unique demands.
Decision Factors
When selecting between cold-formed steel home kits and red iron buildings, key decision factors include cost efficiency, construction timeline, customization options, and long-term durability.
- Cost Efficiency: Cold-formed steel home kits often have shorter delivery times and lower foundation costs than red iron buildings, making them a more cost-effective option for certain projects.
- Construction Timeline: Consider the urgency of the project when deciding between the two options. Cold-formed steel home kits may offer quicker construction timelines due to their prefabricated nature.
- Customization Options: Red iron buildings are more customizable for larger facilities, allowing for greater flexibility in design. Conversely, cold-formed steel home kits provide more tailored solutions to specific needs but may require additional engineering considerations.
Evaluating these factors alongside the project’s requirements, budget constraints, and aesthetic preferences will help you determine the most suitable option between cold-formed steel home kits and red iron buildings.
Advantages Summary
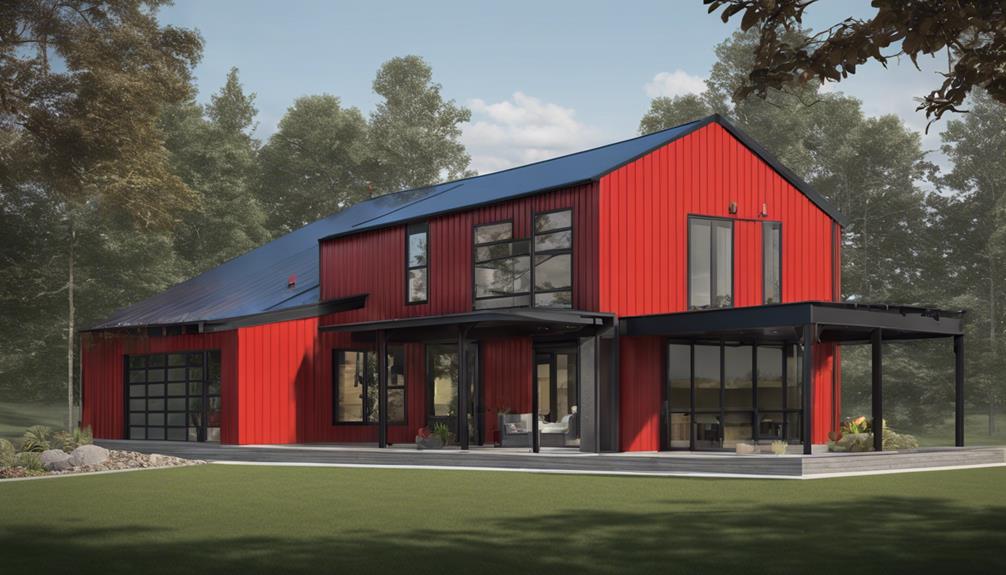
Cold-formed steel home kits offer expedited construction timelines in comparison to red iron buildings. The efficiency of light gauge steel construction allows for quicker project completion, which can be advantageous when time is of the essence. This speed is achieved through the prefabrication of components, reducing on-site construction time to a considerable extent. Additionally, the lightweight nature of cold-formed steel makes it easier to handle and maneuver during the building process, further contributing to the accelerated construction schedule.
On the other hand, red iron buildings excel in providing customization options for structures requiring large open spans, such as gyms or churches. The strength and durability of red iron make it ideal for supporting expansive areas without the need for intermediate columns or supports. While light gauge steel construction offers flexibility in design, red iron buildings shine in their ability to cater to specific architectural requirements for buildings with vast interior spaces. Combining the advantages of both cold-formed steel and red iron can be a strategic approach for projects seeking a balance between speed and customization.
Choosing Your Material
To select the most suitable material for your project, evaluate the structural requirements and design preferences between cold-formed steel home kits and red iron buildings. When deciding between the two options, consider the following:
1. Material Composition:
- Cold-formed steel home kits utilize light gauge steel sheets for framing components.
- Red iron buildings use industrial-grade steel with a red-tinted iron oxide primer.
2. Structural Rigidity:
- Light gauge steel in cold-formed kits is roll-formed to create beams and support structures, offering rigidity against natural disasters.
- Red iron buildings feature large, wide beams to enhance strength and durability.
3. Customization Options:
- Cold-formed steel home kits allow for various cladding types due to standard framing, offering more design flexibility.
- Red iron buildings commonly use steel or aluminum panels for cladding, limiting customization options.
- Understanding these distinctions will help in determining the most suitable material for your project based on structural needs and design preferences.
Frequently Asked Questions
Is Red Iron Better Than Steel?
When evaluating whether red iron is superior to steel, it is crucial to analyze your project’s specific requirements. Red iron structures are appreciated for their durability, affordability, and flexibility in construction. They perform well in large open-span buildings such as gyms or churches. On the other hand, light gauge steel provides more customization options but may necessitate unique engineering solutions. Grasping the unique characteristics of each material will assist you in determining which is most suitable for your project needs.
Why Cold-Formed Steel Frame Components Make a Better Building?
When it comes to why cold-formed steel frame components make a better building, consider the efficiency and versatility they offer. With lighter components reducing shipping and handling costs, along with enhanced durability against rust and moisture, cold-formed steel buildings excel in both aesthetics and longevity. Their design flexibility allows for tailored customization, ensuring that your project meets specific needs with precision and style.
What Is the Best Type of Metal Building?
When selecting the optimal kind of metal building, take into account your project’s specific needs. Evaluate factors such as size, design flexibility, and cost-effectiveness. Understanding the distinctions between various construction methods can assist you in determining the most suitable option. It is crucial to consider the advantages of each type of building system to make certain it aligns with your project goals and requirements. Conduct thorough research to make an informed decision that meets your needs effectively.
What Is the Difference Between Cold-Formed Steel and Steel?
When contemplating the distinction between cold-formed steel and traditional steel, it is crucial to grasp that cold-formed steel is roll-formed into shapes for construction, offering more design flexibility. In contrast, traditional steel, such as red iron steel, is heavier and less adaptable. Cold-formed steel is frequently utilized in residential and light commercial projects due to its lightweight nature, while red iron steel is preferred for its strength in larger industrial and commercial buildings.